Lazer qaynaq
Son illərdə yeni enerji sənayesinin sürətli inkişafı sayəsində lazer qaynağı sürətli və sabit üstünlükləri sayəsində bütün yeni enerji sənayesinə sürətlə nüfuz etmişdir.Onların arasında lazer qaynaq avadanlığı bütün yeni enerji sənayesində tətbiqlərin ən yüksək nisbətini təşkil edir.
Lazer qaynaq sürətli sürəti, böyük dərinliyi və kiçik deformasiyası səbəbindən həyatın bütün sahələrində tez bir zamanda ilk seçim oldu.Nöqtə qaynaqlarından tutmuş qaynaqlara, yığılma və sızdırmazlıq qaynaqlarına qədər lazer qaynağı misilsiz dəqiqlik və nəzarət təmin edir.Sənaye istehsalı və istehsalında, o cümlədən hərbi sənaye, tibbi xidmət, aerokosmik, 3C avtomobil hissələri, mexaniki sac metal, yeni enerji və digər sənaye sahələrində mühüm rol oynayır.
Digər qaynaq texnologiyaları ilə müqayisədə lazer qaynaqının özünəməxsus üstünlükləri və mənfi cəhətləri var.
Üstünlük:
1. Sürətli sürət, böyük dərinlik və kiçik deformasiya.
2. Qaynaq normal temperaturda və ya xüsusi şəraitdə həyata keçirilə bilər və qaynaq avadanlığı sadədir.Məsələn, lazer şüası elektromaqnit sahəsində sürüşmür.Lazerlər vakuumda, havada və ya müəyyən qaz mühitlərində qaynaq edə bilər və şüşədən keçən və ya lazer şüasına şəffaf olan materialları qaynaq edə bilər.
3. Titan və kvars kimi odadavamlı materialları qaynaq edə bilər və eyni zamanda yaxşı nəticələrlə fərqli materialları qaynaq edə bilər.
4. Lazer fokuslandıqdan sonra güc sıxlığı yüksək olur.Aspekt nisbəti 5: 1-ə çata bilər və yüksək güclü cihazları qaynaq edərkən 10: 1-ə çata bilər.
5. Mikro qaynaq həyata keçirilə bilər.Lazer şüası fokuslandıqdan sonra kiçik bir nöqtə əldə edilə və dəqiq şəkildə yerləşdirilə bilər.Avtomatlaşdırılmış kütləvi istehsala nail olmaq üçün mikro və kiçik iş parçalarının yığılması və qaynaqlanması üçün tətbiq oluna bilər.
6. Böyük çevikliklə çatmaq çətin olan yerləri qaynaq edə və təmassız uzun məsafəli qaynaqları yerinə yetirə bilər.Xüsusilə son illərdə YAG lazer emal texnologiyası lazer qaynaq texnologiyasının daha geniş şəkildə təbliğinə və tətbiqinə imkan verən optik lif ötürmə texnologiyasını qəbul etmişdir.
7. Lazer şüasını zaman və məkanda bölmək asandır və birdən çox şüa eyni vaxtda bir neçə yerdə işlənə bilər ki, bu da daha dəqiq qaynaq üçün şərait yaradır.
Qüsur:
1. İş parçasının yığılma dəqiqliyinin yüksək olması tələb olunur və iş parçası üzərində şüanın mövqeyi əhəmiyyətli dərəcədə kənara çıxa bilməz.Bunun səbəbi, fokuslandıqdan sonra lazer nöqtəsinin ölçüsünün kiçik olması və qaynaq tikişinin dar olmasıdır, bu da doldurucu metal materialların əlavə edilməsini çətinləşdirir.İş parçasının montaj dəqiqliyi və ya şüanın yerləşdirilməsinin dəqiqliyi tələblərə cavab vermirsə, qaynaq qüsurları meydana gəlməyə meyllidir.
2. Lazerlərin və əlaqəli sistemlərin qiyməti yüksəkdir və birdəfəlik investisiya böyükdür.
Litium batareya istehsalında ümumi lazer qaynaq qüsurları
1. Qaynaq məsaməliliyi
Lazer qaynaqında ümumi qüsurlar məsamələrdir.Qaynaq əridilmiş hovuz dərin və dardır.Lazer qaynaq prosesi zamanı azot xaricdən ərimiş hovuza daxil olur.Metalın soyuması və bərkiməsi prosesində temperaturun azalması ilə azotun həllolma qabiliyyəti azalır.Ərinmiş hovuz metalı kristallaşmağa başlamaq üçün soyuduqda, həlledicilik kəskin və birdən düşəcək.Bu zaman çoxlu miqdarda qaz çökəcək və qabarcıqlar əmələ gələcək.Baloncukların üzmə sürəti metalın kristallaşma sürətindən az olarsa, məsamələr əmələ gələcək.
Litium batareya sənayesindəki tətbiqlərdə biz tez-tez məsamələrin müsbət elektrodun qaynağı zamanı meydana çıxma ehtimalı olduğunu, lakin mənfi elektrodun qaynağı zamanı nadir hallarda baş verdiyini görürük.Bunun səbəbi müsbət elektrodun alüminiumdan, mənfi elektrodun isə misdən olmasıdır.Qaynaq zamanı səthdə olan maye alüminium daxili qaz tamamilə daşmazdan əvvəl qatılaşaraq qazın daşması və irili-xırdalı deşiklərin əmələ gəlməsinin qarşısını alır.Kiçik stomalar.
Məsamələrə yuxarıda qeyd olunan səbəblərdən əlavə, həmçinin açıq hava, rütubət, səth yağı və s. daxildir. Bundan əlavə, azotun üfürülməsinin istiqaməti və bucağı da məsamələrin əmələ gəlməsinə təsir edəcəkdir.
Qaynaq məsamələrinin meydana gəlməsini necə azaltmaq olar?
Birincisi, qaynaqdan əvvəl, daxil olan materialların səthindəki yağ ləkələri və çirkləri vaxtında təmizləmək lazımdır;litium batareyalarının istehsalında daxil olan materialın yoxlanılması vacib bir prosesdir.
İkincisi, qoruyucu qaz axını qaynaq sürəti, güc, mövqe və s. kimi amillərə uyğun olaraq tənzimlənməlidir və nə çox böyük, nə də çox kiçik olmamalıdır.Qoruyucu örtük təzyiqi lazer gücü və fokus mövqeyi kimi amillərə uyğun olaraq tənzimlənməlidir və nə çox yüksək, nə də çox aşağı olmamalıdır.Qoruyucu plaşın başlığının forması qaynağın formasına, istiqamətinə və digər amillərə uyğun olaraq tənzimlənməlidir ki, qoruyucu plaş qaynaq sahəsini bərabər şəkildə örtsün.
Üçüncüsü, atelyedə havanın temperaturu, rütubəti və tozuna nəzarət edin.Ətraf mühitin temperaturu və rütubəti substratın səthindəki rütubətə və qoruyucu qaza təsir edəcək, bu da öz növbəsində ərimiş hovuzda su buxarının yaranmasına və çıxmasına təsir edəcəkdir.Ətraf mühitin temperaturu və rütubəti çox yüksək olarsa, substratın və qoruyucu qazın səthində çox nəm olacaq, çox miqdarda su buxarı əmələ gəlir və nəticədə məsamələr yaranır.Ətraf mühitin temperaturu və rütubəti çox aşağı olarsa, substratın səthində və qoruyucu qazda çox az nəm olacaq, su buxarının əmələ gəlməsini azaldır və bununla da məsamələri azaldır;keyfiyyət işçiləri qaynaq stansiyasında temperaturun, rütubətin və tozun hədəf dəyərini aşkar etsinlər.
Dördüncüsü, şüa yelləncək üsulu lazer dərin nüfuz qaynaqında məsamələri azaltmaq və ya aradan qaldırmaq üçün istifadə olunur.Qaynaq zamanı yelləncək əlavə edildiyinə görə, şüanın qaynaq tikişinə qarşılıqlı yellənməsi qaynaq tikişinin bir hissəsinin təkrar əriməsinə səbəb olur ki, bu da maye metalın qaynaq hovuzunda qalma müddətini uzadır.Eyni zamanda, şüanın əyilməsi də vahid sahəyə istilik girişini artırır.Qaynaq tikişinin dərinliyin eninə nisbəti azalır, bu da baloncukların yaranmasına şərait yaradır və bununla da məsamələri aradan qaldırır.Digər tərəfdən, şüanın yellənməsi kiçik çuxurun müvafiq olaraq yellənməsinə səbəb olur ki, bu da qaynaq hovuzu üçün bir qarışdırıcı qüvvə təmin edə, qaynaq hovuzunun konveksiyasını və qarışdırılmasını artıra bilər və məsamələrin aradan qaldırılmasına faydalı təsir göstərə bilər.
Beşincisi, nəbz tezliyi, nəbz tezliyi, eritilmiş hovuzda istilik girişinə və istilik yığılmasına təsir edəcək və sonra ərimiş hissədə temperatur sahəsinə və axın sahəsinə təsir edəcək vahid vaxtda lazer şüası tərəfindən buraxılan impulsların sayına aiddir. hovuz.Nəbz tezliyi çox yüksək olarsa, bu, ərimiş hovuzda həddindən artıq istilik daxil olmasına gətirib çıxaracaq, ərimiş hovuzun temperaturunun çox yüksək olmasına səbəb olacaq, metal buxarı və ya yüksək temperaturda uçucu olan digər elementlər əmələ gələcək və nəticədə məsamələr yaranacaq.Nəbz tezliyi çox aşağı olarsa, bu, ərimiş hovuzda qeyri-kafi istilik yığılmasına gətirib çıxaracaq, ərimiş hovuzun temperaturunun çox aşağı olmasına səbəb olur, qazın həllini və qaçmasını azaldır, nəticədə məsamələr yaranır.Ümumiyyətlə, nəbz tezliyi substratın qalınlığına və lazer gücünə əsaslanaraq ağlabatan diapazonda seçilməli və çox yüksək və ya çox aşağı olmamalıdır.
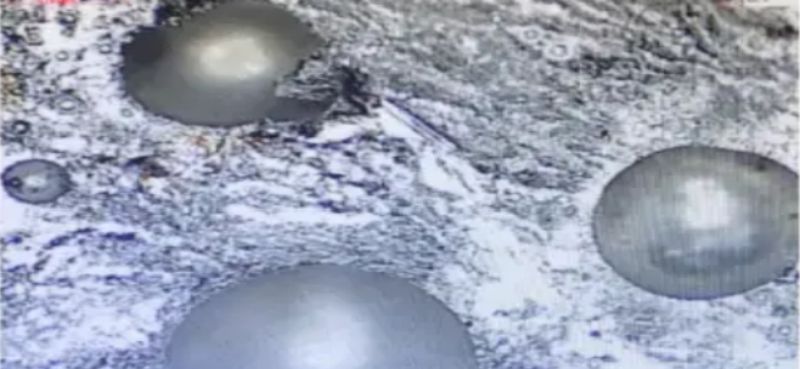
Qaynaq deşikləri (lazer qaynağı)
2. Qaynaq sıçratması
Qaynaq prosesi zamanı əmələ gələn sıçrayış, lazer qaynağı qaynağın səth keyfiyyətinə ciddi təsir edəcək, linzaları çirkləndirəcək və zədələyəcək.Ümumi performans aşağıdakı kimidir: lazer qaynağı başa çatdıqdan sonra materialın və ya iş parçasının səthində çoxlu metal hissəciklər görünür və materialın və ya iş parçasının səthinə yapışır.Ən intuitiv performans ondan ibarətdir ki, galvanometrin rejimində qaynaq edərkən, qalvanometrin qoruyucu lensindən bir müddət istifadə edildikdən sonra səthdə sıx çuxurlar olacaq və bu çuxurlar qaynaq sıçraması nəticəsində yaranır.Uzun müddətdən sonra işığın qarşısını almaq asandır və qaynaq işığında problemlər yaranacaq, nəticədə qırıq qaynaq və virtual qaynaq kimi bir sıra problemlər yaranacaq.
Sıçrama səbəbləri nələrdir?
Birincisi, güc sıxlığı, güc sıxlığı nə qədər böyükdürsə, sıçrayış yaratmaq daha asan olur və sıçrayış birbaşa güc sıxlığı ilə bağlıdır.Bu bir əsrlik problemdir.Ən azı indiyə qədər sənaye sıçrama problemini həll edə bilmədi və yalnız bir az azaldıldığını söyləyə bilər.Litium batareya sənayesində sıçrama batareyanın qısa qapanmasının ən böyük günahkarıdır, lakin əsas səbəbi həll edə bilməyib.Sıçrayışın batareyaya təsiri yalnız qorunma baxımından azaldıla bilər.Məsələn, qaynaq hissəsinin ətrafına bir dairə tozdan təmizləyici portlar və qoruyucu örtüklər əlavə olunur və sıçrayışın təsirinin qarşısını almaq və hətta batareyaya zərər verməmək üçün hava bıçaqlarının sıraları dairələrə əlavə olunur.Qaynaq stansiyasının ətrafındakı ətraf mühitin, məhsulların və komponentlərin məhv edilməsi vasitələrin tükəndiyini söyləmək olar.
Sıçrama probleminin həllinə gəlincə, yalnız qaynaq enerjisinin azaldılmasının sıçrayışın azalmasına kömək etdiyini söyləmək olar.Nüfuz kifayət deyilsə, qaynaq sürətinin azaldılması da kömək edə bilər.Ancaq bəzi xüsusi proses tələblərində az təsir göstərir.Eyni prosesdir, müxtəlif maşınlar və müxtəlif material partiyaları tamamilə fərqli qaynaq effektlərinə malikdir.Buna görə də, yeni enerji sənayesində yazılmamış bir qayda var, bir avadanlıq üçün bir qaynaq parametrləri toplusu.
İkincisi, işlənmiş materialın və ya iş parçasının səthi təmizlənməsə, yağ ləkələri və ya çirkləndiricilər də ciddi sıçramalara səbəb olacaqdır.Bu zaman ən asan iş işlənmiş materialın səthini təmizləməkdir.
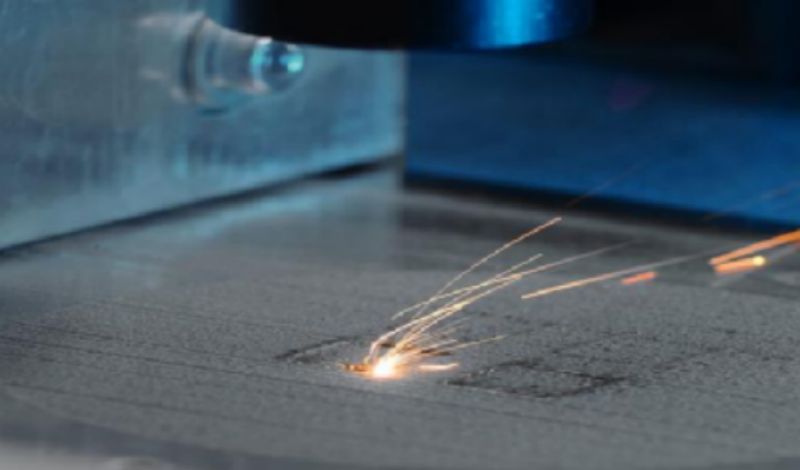
3. Lazer qaynaqının yüksək əks etdirmə qabiliyyəti
Ümumiyyətlə, yüksək əks etdirmə dedikdə, emal materialının kiçik müqavimətə, nisbətən hamar bir səthə və yaxın infraqırmızı lazerlər üçün aşağı udma dərəcəsinə malik olması nəzərdə tutulur ki, bu da böyük miqdarda lazer emissiyasına səbəb olur və əksər lazerlər istifadə olunur. şaquli olaraq Materiala və ya az miqdarda meylə görə, geri qayıdan lazer işığı yenidən çıxış başlığına daxil olur və hətta geri dönən işığın bir hissəsi enerji ötürücü lifə birləşdirilir və lif boyunca içəriyə geri ötürülür. lazerin içindəki əsas komponentlər yüksək temperaturda olmağa davam edir.
Lazer qaynağı zamanı əks etdiricilik çox yüksək olduqda, aşağıdakı həllər qəbul edilə bilər:
3.1 Yansıtma əleyhinə örtükdən istifadə edin və ya materialın səthini müalicə edin: qaynaq materialının səthini əks etdirməyə qarşı örtüklə örtmək lazerin əks olunma qabiliyyətini effektiv şəkildə azalda bilər.Bu örtük adətən lazer enerjisini geri əks etdirmək əvəzinə udan, əks etdirmə qabiliyyəti aşağı olan xüsusi optik materialdır.Bəzi proseslərdə, məsələn, cərəyan kollektorunun qaynaqlanması, yumşaq birləşmə və s., səthi də qabartmaq olar.
3.2 Qaynaq bucağını tənzimləyin: Qaynaq bucağını tənzimləməklə, lazer şüası qaynaq materialına daha uyğun bucaq altında düşə bilər və əksin baş verməsini azalda bilər.Normalda, lazer şüasının qaynaq ediləcək materialın səthinə perpendikulyar düşməsi əksi azaltmaq üçün yaxşı bir yoldur.
3.3 Köməkçi absorbentin əlavə edilməsi: Qaynaq prosesi zamanı qaynağa müəyyən miqdarda köməkçi uducu, məsələn, toz və ya maye əlavə edilir.Bu absorberlər lazer enerjisini udur və əks etdirmə qabiliyyətini azaldır.Xüsusi qaynaq materialları və tətbiq ssenariləri əsasında müvafiq absorbent seçilməlidir.Litium batareya sənayesində bu mümkün deyil.
3.4 Lazeri ötürmək üçün optik lifdən istifadə edin: Mümkünsə, əks etdirmə qabiliyyətini azaltmaq üçün lazeri qaynaq mövqeyinə ötürmək üçün optik lifdən istifadə oluna bilər.Optik liflər, qaynaq materialının səthinə birbaşa məruz qalmamaq və yansımaların baş verməsini azaltmaq üçün lazer şüasını qaynaq sahəsinə yönəldə bilər.
3.5 Lazer parametrlərinin tənzimlənməsi: Lazer gücü, fokus uzunluğu və fokus diametri kimi parametrləri tənzimləməklə lazer enerjisinin paylanmasına nəzarət etmək və əksetmələri azaltmaq olar.Bəzi əks etdirən materiallar üçün lazer gücünün azaldılması əksetmələri azaltmaq üçün təsirli bir yol ola bilər.
3.6 Şüa ayırıcıdan istifadə edin: Şüa ayırıcı lazer enerjisinin bir hissəsini udma qurğusuna yönəldə bilər və bununla da əks olunmaların baş verməsini azaldır.Şüa parçalayıcı qurğular adətən optik komponentlərdən və absorberlərdən ibarətdir və müvafiq komponentləri seçmək və cihazın sxemini tənzimləməklə daha aşağı əks etdirmə qabiliyyətinə nail olmaq olar.
4. Qaynaq altlığı
Litium batareyalarının istehsal prosesində hansı proseslərin kəsilməyə səbəb olma ehtimalı daha yüksəkdir?Niyə alt kəsmə baş verir?Gəlin bunu təhlil edək.
Kəsilmiş, ümumiyyətlə qaynaq xammalı bir-biri ilə yaxşı birləşmir, boşluq çox böyükdür və ya yiv görünür, dərinlik və eni əsasən 0,5 mm-dən çoxdur, ümumi uzunluq qaynaq uzunluğunun 10% -dən çoxdur və ya tələb olunan uzunluq məhsul prosesi standartından böyükdür.
Bütün litium batareyanın istehsal prosesində alt kəsmə baş vermə ehtimalı daha yüksəkdir və ümumiyyətlə silindrik örtük plitəsinin möhürlənməsinin əvvəlcədən qaynaqlanması və qaynaqlanması və kvadrat alüminium qabığın qapaq plitəsinin möhürlənməsinin əvvəlcədən qaynaqlanması və qaynaqlanmasında paylanır.Əsas səbəb odur ki, möhürləyici örtük lövhəsi Qaynaq üçün qabıqla əməkdaşlıq etməlidir, sızdırmazlıq örtüyü lövhəsi ilə qabıq arasında uyğunlaşma prosesi həddindən artıq qaynaq boşluqlarına, yivlərə, çökməyə və s. .
Beləliklə, kəsilmənin səbəbi nədir?
Qaynaq sürəti çox sürətli olarsa, qaynağın mərkəzinə işarə edən kiçik çuxurun arxasındakı maye metal yenidən paylanmağa vaxt tapmayacaq, nəticədə qaynağın hər iki tərəfində bərkimə və alt kəsmə baş verir.Yuxarıdakı vəziyyəti nəzərə alaraq, qaynaq parametrlərini optimallaşdırmalıyıq.Sadə dillə desək, bu, müxtəlif parametrləri yoxlamaq üçün təkrar təcrübələrdir və müvafiq parametrlər tapılana qədər DOE-ni davam etdirir.
2. Qaynaq materiallarının həddindən artıq qaynaq boşluqları, yivləri, çökmələri və s. boşluqları dolduran ərimiş metalın miqdarını azaldacaq, alt kəsiklərin baş vermə ehtimalını artıracaqdır.Bu, avadanlıq və xammal məsələsidir.Qaynaq xammalının prosesimizin daxil olan material tələblərinə cavab verib-verməməsi, avadanlığın dəqiqliyinin tələblərə uyğun olub-olmaması və s. Normal təcrübə təchizatçılara və avadanlıqlara cavabdeh olan şəxslərə daim işgəncə vermək və döyməkdir.
3. Lazer qaynaqının sonunda enerji çox sürətlə aşağı düşərsə, kiçik dəlik çökə bilər və nəticədə yerli alt kəsmə baş verə bilər.Gücün və sürətin düzgün uyğunluğu alt kəsiklərin əmələ gəlməsinin qarşısını effektiv şəkildə ala bilər.Köhnə deyimdə deyildiyi kimi, təcrübələri təkrarlayın, müxtəlif parametrləri yoxlayın və düzgün parametrləri tapana qədər DOE-yə davam edin.
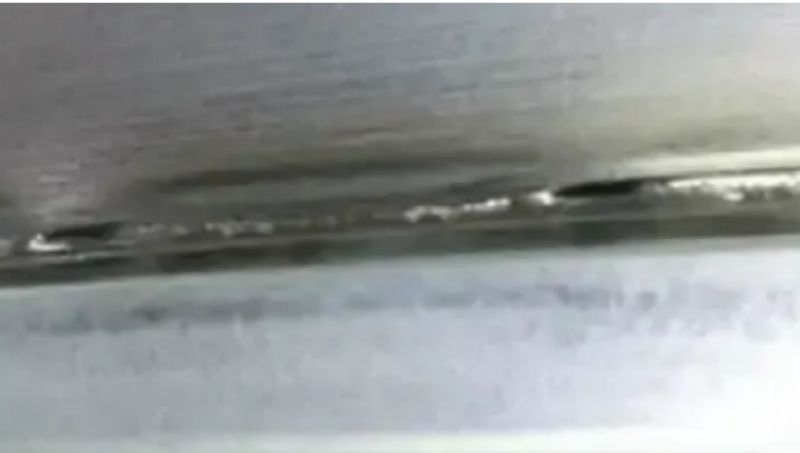
5. Qaynaq mərkəzinin çökməsi
Qaynaq sürəti yavaş olarsa, ərimiş hovuz daha böyük və daha geniş olacaq, ərimiş metalın miqdarı artır.Bu, səthi gərginliyin saxlanmasını çətinləşdirə bilər.Ərinmiş metal çox ağırlaşdıqda, qaynağın mərkəzi bataraq çuxurlar və çuxurlar əmələ gətirə bilər.Bu halda, ərimə hovuzunun çökməsinin qarşısını almaq üçün enerji sıxlığını müvafiq şəkildə azaltmaq lazımdır.
Başqa bir vəziyyətdə, qaynaq boşluğu perforasiyaya səbəb olmadan sadəcə bir çökmə meydana gətirir.Bu, şübhəsiz ki, avadanlığın mətbuata uyğunluğu problemidir.
Lazer qaynağı zamanı baş verə biləcək qüsurları və müxtəlif qüsurların səbəblərini düzgün başa düşmək hər hansı anormal qaynaq problemlərini həll etmək üçün daha məqsədyönlü yanaşmaya imkan verir.
6. Qaynaq çatları
Davamlı lazer qaynağı zamanı yaranan çatlar əsasən kristal çatlar və mayeləşmə çatları kimi termal çatlardır.Bu çatların əsas səbəbi qaynaq tikişinin tam bərkimədən əvvəl yaratdığı böyük büzülmə qüvvələridir.
Lazer qaynaqında çatların aşağıdakı səbəbləri də var:
1. Məntiqsiz qaynaq dizaynı: Qaynaq tikişinin həndəsəsinin və ölçüsünün düzgün tərtib edilməməsi qaynaq gərginliyinin konsentrasiyasına səbəb ola bilər və bununla da çatlara səbəb ola bilər.Həll, qaynaq gərginliyinin konsentrasiyasının qarşısını almaq üçün qaynaq dizaynını optimallaşdırmaqdır.Siz uyğun ofset qaynaqlarından istifadə edə, qaynaq formasını dəyişdirə və s.
2. Qaynaq parametrlərinin uyğunsuzluğu: Qaynaq parametrlərinin düzgün seçilməməsi, məsələn, çox sürətli qaynaq sürəti, çox yüksək güc və s., qaynaq sahəsində qeyri-bərabər temperatur dəyişikliklərinə səbəb ola bilər, nəticədə böyük qaynaq gərginliyi və çatlar yarana bilər.Həll xüsusi material və qaynaq şərtlərinə uyğun olaraq qaynaq parametrlərini tənzimləməkdir.
3. Qaynaq səthinin zəif hazırlanması: Qaynaqdan əvvəl qaynaq səthinin düzgün təmizlənməməsi və əvvəlcədən müalicə edilməməsi, məsələn, oksidlərin, yağların və s. təmizlənməsi qaynağın keyfiyyətinə və möhkəmliyinə təsir edəcək və asanlıqla çatlara səbəb olacaqdır.Həll qaynaq sahəsindəki çirklərin və çirkləndiricilərin effektiv şəkildə təmizlənməsini təmin etmək üçün qaynaq səthini adekvat təmizləmək və əvvəlcədən müalicə etməkdir.
4. Qaynaq istiliyinin daxilinə düzgün nəzarət edilməməsi: Qaynaq zamanı daxil olan istilik miqdarına zəif nəzarət, məsələn, qaynaq zamanı həddindən artıq temperatur, qaynaq təbəqəsinin düzgün soyuma sürəti və s., qaynaq sahəsinin strukturunun dəyişməsinə, nəticədə çatların yaranmasına səbəb olacaq. .Həll yolu, həddindən artıq istiləşmədən və sürətli soyutmadan qaçmaq üçün qaynaq zamanı temperatur və soyutma sürətinə nəzarət etməkdir.
5. Qeyri-kafi gərginliyin aradan qaldırılması: Qaynaqdan sonra qeyri-kafi gərginliyin aradan qaldırılması, qaynaqlanmış sahədə kifayət qədər gərginliyin aradan qaldırılması ilə nəticələnəcək və bu, asanlıqla çatlara səbəb olacaqdır.Həll yolu, qaynaqdan sonra istilik müalicəsi və ya vibrasiya müalicəsi (əsas səbəb) kimi müvafiq stress relyef müalicəsini yerinə yetirməkdir.
Litium batareyalarının istehsal prosesinə gəlincə, hansı proseslər daha çox çatlara səbəb olur?
Ümumiyyətlə, silindrik polad qabıqların və ya alüminium qabıqların möhürlənməsi qaynağı, kvadrat alüminium qabıqların möhürlənməsi qaynağı və s. kimi plomb qaynağı zamanı çatlar meydana gəlməyə meyllidir. Bundan əlavə, modulun qablaşdırılması prosesi zamanı cari kollektorun qaynağı da meyllidir. çatlara.
Əlbəttə ki, bu çatları azaltmaq və ya aradan qaldırmaq üçün doldurucu tel, ön qızdırma və ya digər üsullardan da istifadə edə bilərik.
Göndərmə vaxtı: Sentyabr-01-2023